Aug 14, 2024
We built HashyLink, an app for Harvest Right freeze dryers that lets you do detailed batch analytics from any device. No more wasting time with USB sticks and excel if you want to do batch analytics and find efficiency.
For the first time ever, you've got easy access to your Harvest Right logs. We know it can be a lot to take in at first, so we put together this quick guide on what to look for in your batch graphs.
We're constantly discovering new ways to make this more useful, so if you have any suggestions or find any patterns, let us know and it might become a feature.
Understanding Your Batch Breakdown Screen
When you open your batch breakdown screen, you'll see the entire timeline of your freeze dryer run, neatly broken down into stages:
Freeze
Vacuum freeze
Dry cycles
Final dry cycles
Defrost
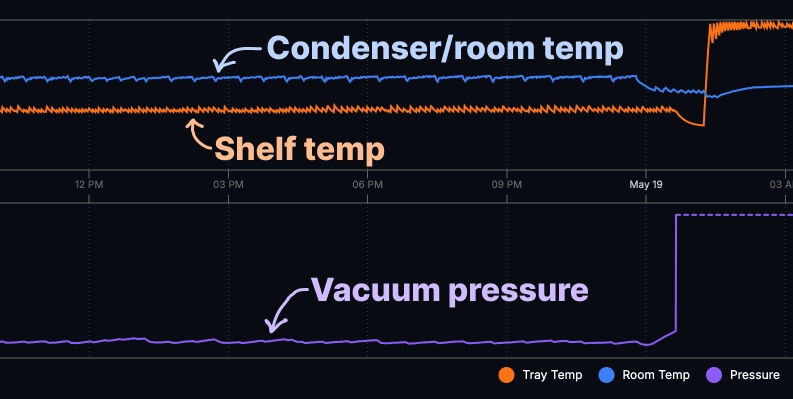
The key elements to focus on are:
Condenser/room temperatures (blue line)
Shelf temperatures (orange line)
Vacuum pressure levels (purple line)
Let's dive deeper into each of these metrics and how they can impact your freeze drying.
Condenser/Room Temperature (Blue Line)
The blue line represents both condenser and room temperature. The sensor for room temp sits right next to your condenser, giving you an amalgamation of the two.
What to look for:
Environmental performance: This is crucial, especially for high-production labs.
Impact on batch Times: Running multiple freeze dryers without ideal heat management? You could be losing serious time on your batches.
We've seen batch times impacted by as much as 40% when environmental parameters aren't ideal. HashyLink allows you to:
Observe how condenser and room temps impact your batches over time
Find the optimal placement for your freeze dryers
Improve airflow to reduce batch times
Condenser Spike

In this example of a condenser spike, you'll notice the condenser trending a bit high but mostly flat. Then, as the shelves heat up for drying, there's a massive spike. The shelves lose temperature, kick back into freezing, and you get a bit more drying action.
This interrupts your batch significantly. When you spot something like this, consider:
Did someone accidentally switch it back to freezing?
Is this a machine glitch?
What could have caused this interruption?
Remember, you're aiming for a stable, consistent line throughout your batch.
Shelf Temperature (Orange Line)
The orange line shows your Harvest Right's shelf temperature - that's the heat applied to your product during primary and secondary drying.
What to look for:
A stable, steady line
Large swings or spikes may indicate an issue with your freeze dryer or batch sizing
Typical pattern

In this batch, you can see a stable consistent line that doesn't swing by more than a few degrees throughout the run. This indicates stable shelf temps with proper batch sizing and nothing to be alarmed about.
Abnormal pattern
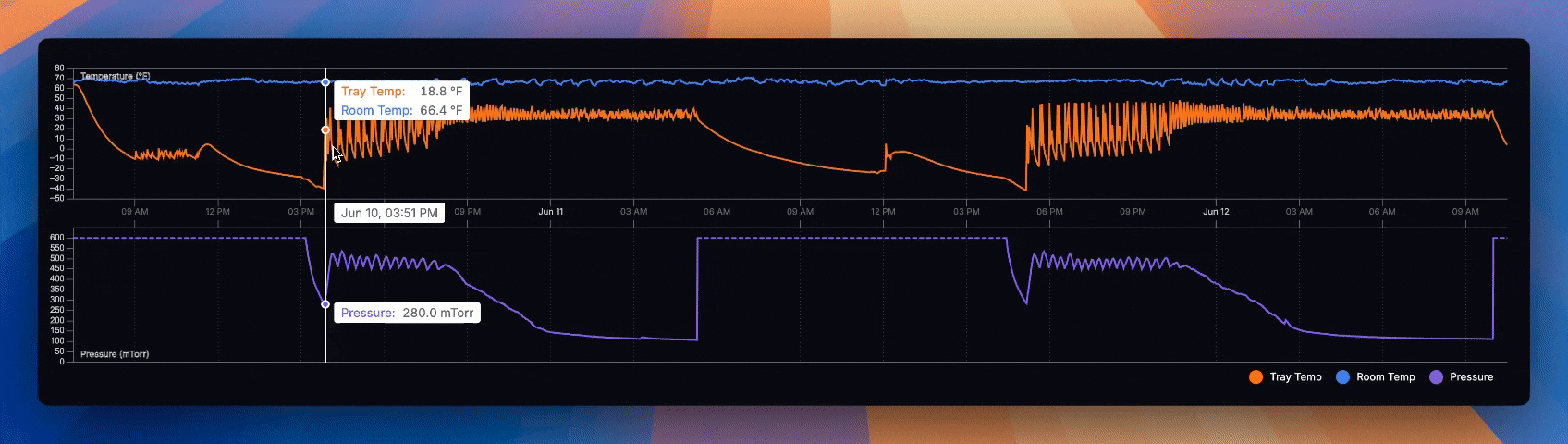
This is an abnormal pattern. Swings over 20 degrees like this could indicate:
Hardware issues
Environmental parameter problems
Batch size issues leading to uneven heat application
Big spikes might indicate uneven drying. This is your cue to start experimenting.
Test different temperatures and observe their performance on the graph.
Note how different batch sizes or types of resin react to various shelf temps.
Use your logs to see how batch sizes and shelf temps are related.
Large swings might mean you need to dry more material at once.
If larger batches aren't possible, try compensating with lower shelf temps. The key is to monitor those swings and adjust as needed.
Vacuum Pressure (Purple Line)
For vacuum pressure, look for a steady initial drop followed by consistent levels during drying.
Vacuum Freezing
If you're hanging around the initial pressure for a long time before it starts dropping, it might indicate something wrong with seals or the pump.
Middle of Drying Cycles
Spikes and hills could indicate that your environment is getting too hot and your components are getting overworked.
You shouldn't see much change in the middle of the batch until the hash is done, then pressure will stabilize.
Batch Completion
Some users report seeing vacuum pressures stabilize when the batch is done, but it's hard to say definitively without consistently measuring your starting weights and timing your batches/keeping sizes consistent.
Let us know if you see any patterns in the graphs when you detect doneness - we might add it as a future feature!
Quick Spikes
When you see quick spikes in vacuum pressure, it usually means that you popped the door open to check your hash or swap trays.
Quick spikes mid-batch
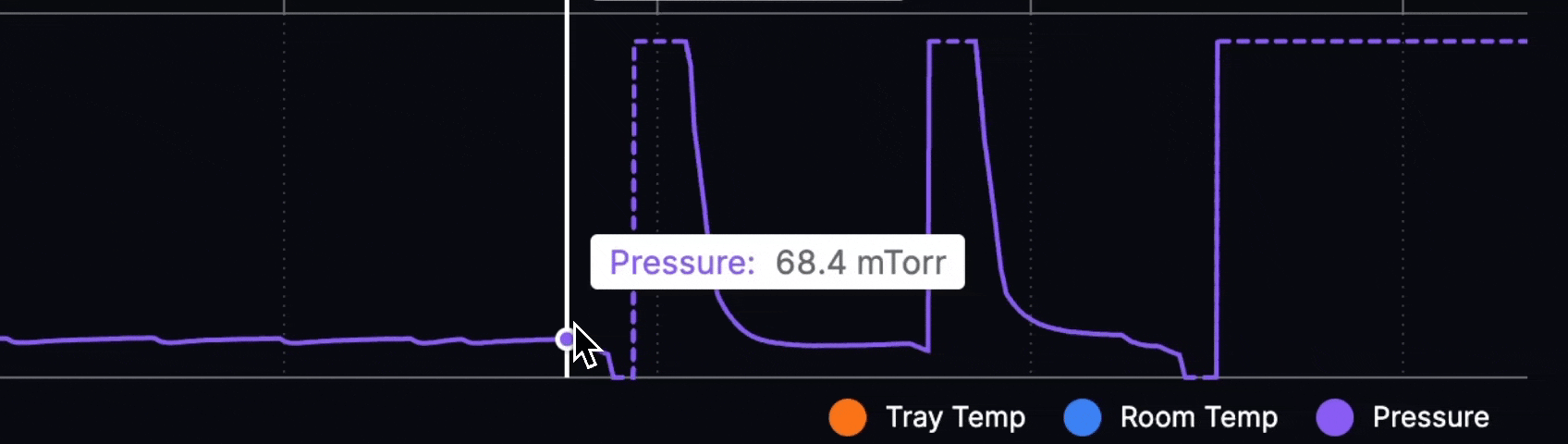
Quick spikes like this typically indicate checking your batch mid-run. This will help you track how many times you checked your batch, what impact that had on time, and develop an understanding of when your hash is ready on a run by run basis.
Quick spikes at end of batch

This generally indicates the last time that you checked a batch and pulled your trays out.
These are just a few key things you can look at using HashyLink logs. We're constantly learning from our users about new ways they're leveraging this data to optimize their processes. If you spot any interesting patterns or have ideas for new features, please let us know - there's a good chance we may develop your idea into an actual feature!
Advanced Analytics: Detecting Batch Completion
As you become more familiar with your batch graphs, you'll start noticing subtle cues that indicate your batch is nearing completion.
Using Vacuum Levels
Some users report detecting dryness by observing when their vacuum levels start to even out. Keep an eye on that purple line towards the end of your batch.
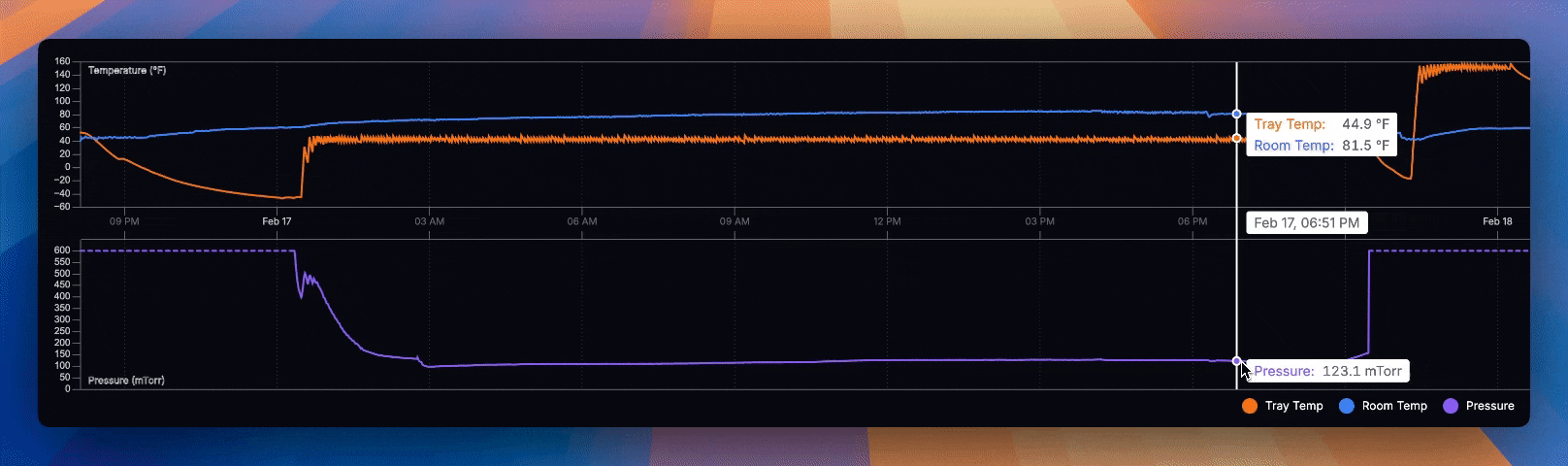
Above, you can see how vacuum levels will flatten over time before reaching a low point. Some users have reported that looking at this leveling out helps them determine dryness. In this example, you can see three batches with similar vacuum plateaus towards the end of the cycle, before the hash was dry and removed.
Slight shelf temperature rises may also indicate doneness
Others have noticed a slight rise in shelf temp as drying concludes.
A slight increase in shelf temps towards the end
A tighter coupling of your low and high setpoints
This occurs because there's less moisture in the material, indicating ideal dryness. Less moisture means faster heat transfer, leading to more stable shelf temps and potentially an increase towards the end as there's less material to buffer the heat.
Leveling Up Your Hash Game
Understanding these metrics is key to achieving batch-to-batch consistency and diving deep into what your hash is doing at every stage.
Level 1: Dial in your recipe and ensure your hash comes out fire
Level 2: Take an iterative approach to understand what levers you can pull for different results
We're always excited to discover new ways people are using HashyLink to fine-tune their process. Got a use case we didn't cover here? Hit us up - we might just build a feature out of it!
Coming Soon
We're hard at work on our new batch detection system, which will make our reporting even more accurate across a wider variety of systems and firmware versions.
Support for Holland Green Science freeze dryers
Want to be an early tester? Fill out the form below to join our beta list. We're currently testing a batch visualizer app for Holland Green Science logs, similar to what you see in the analytics features above.
Send us a message with your logs if you want to take it for a spin.